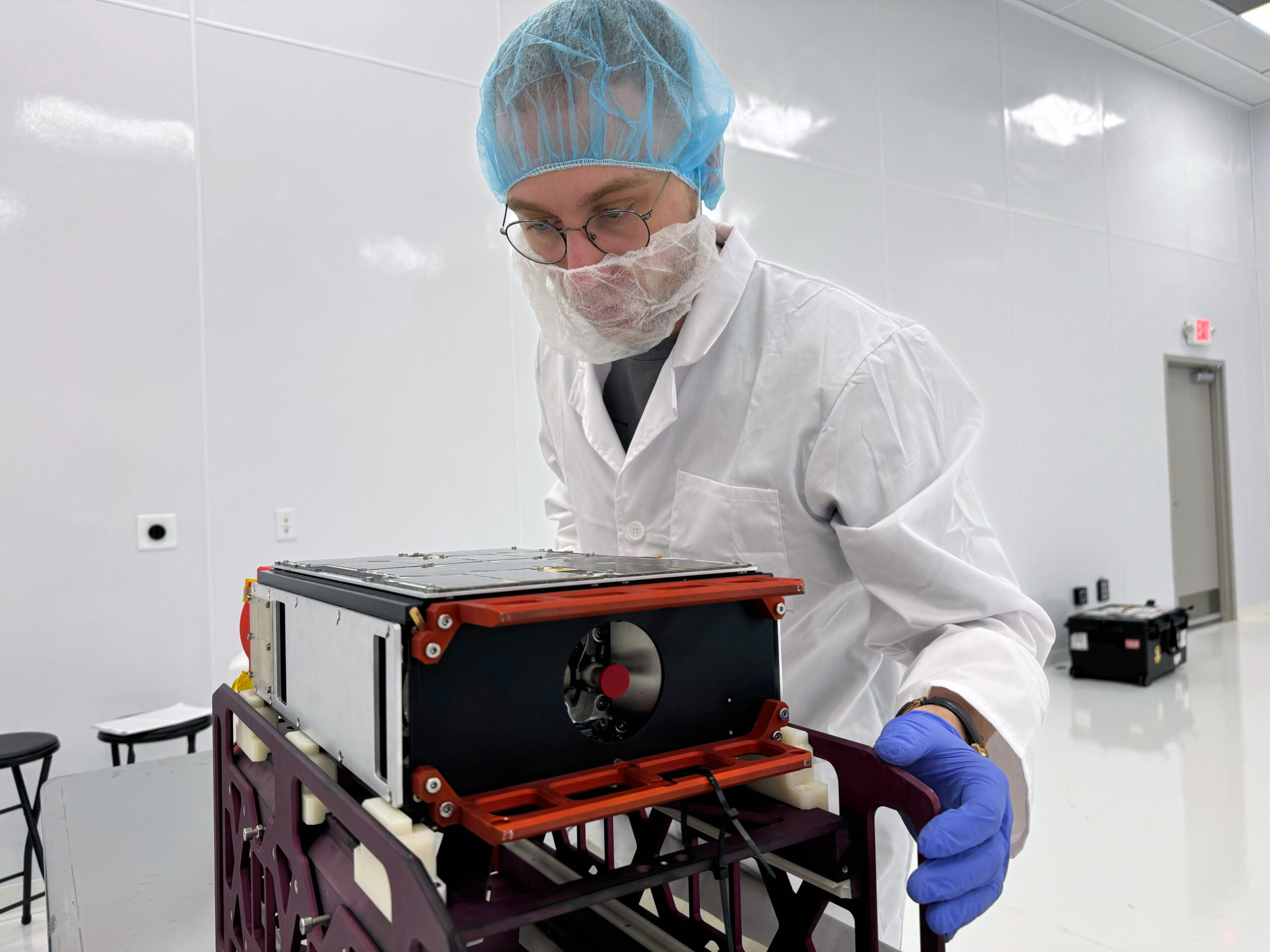
From Idea to Orbit
In just a few weeks, BOOSTER, our propulsion system built from scratch, will fire in space for the first time. It’s surreal—but getting here was anything but easy. Taking an idea from a whiteboard to a working prototype is tough. Turning it into a flight-ready product? Even tougher.
Why Satellite Propulsion Needed a Rethink
Satellite propulsion has long required a trade-off between speed and efficiency. Electric propulsion, while highly efficient, produces low thrust, making orbit changes painfully slow—sometimes taking weeks or months and eating into valuable mission time. In contrast, chemical propulsion offers high thrust for rapid maneuvers but has traditionally been viewed as inefficient. However, with declining launch costs, satellite operators can afford to take more propellant onboard, making efficiency less critical and leading to renewed interest in high-thrust chemical propulsion.
Yet, propulsion isn’t just slow in space. It’s slow to build. Traditional systems take years to develop, test, and integrate, delaying missions and driving up costs. The industry moves fast—propulsion needs to keep up.
That’s why we built BOOSTER. Designed for speed, it slashes lead times from a year to three months. From RFQ to offer in a day, from order to flight-ready in record time—BOOSTER removes the bottlenecks holding space missions back.
And it doesn’t stop there. BOOSTER delivers high thrust for rapid orbital adjustments, collision avoidance, and station-keeping—without the sluggishness of electric propulsion. We engineered steady-state combustion chamber cooling to prevent thermal disruption and adopted green propellants to cut fueling costs and simplify logistics.
The industry is moving fast, and propulsion needs to keep up.
The Road to Flight Wasn’t Easy
Building a propulsion system from scratch isn’t just an engineering challenge—it’s a constant balancing act between physics, budgets, and time.
Funding was the first major hurdle. Unlike software startups, space hardware requires significant capital upfront. We weren’t just funding R&D—we needed to launch a full space mission. We secured funding in May 2023 from three VCs. That was the first step, but it came with a reality check: every dollar had to be spent efficiently.
The real challenge, however, was getting the system to work. Pushing the limits of combustion efficiency, heat management, and system reliability meant a grueling process of trial and error.
The first tests were frustrating. Fixing one issue often created new ones, like untangling a tight knot—every pull only made it worse. Overheating in the combustion chamber led to ignition electrode degradation, which in turn affected the HV ignition system, making repeatability nearly impossible.
Then there were the more dramatic failures—a couple of explosions (CATO) caused by a faulty check valve. Anticipating these risks, we had built a high-durability test stand, capable of dumping 33,000 liters of CO₂ into the chamber within seconds to suppress failures. That decision paid off.
After tens of thousands of test firings and dozens of thruster chamber iterations, things finally stabilized. What started as an experiment was now a working propulsion system, ready to be put to the test in space.
Now, It’s Time for the Real Test
In just days, BOOSTER will undergo its first orbital test. SpaceX’s Falcon 9 will take it to orbit, where the commissioning process will begin. Within weeks, we’ll receive the first data.
Space is unpredictable. Failure is not only an option—but it’s part of the process. Developing this system on a tight timeline and budget meant making trade-offs and focusing on speed. Unlike traditional space agencies with years of development cycles and deep funding, we had to move fast and adapt.
We’ve mapped out every possible outcome—from total failure to full mission success. Regardless of the result, this demonstration will provide valuable data to refine and improve our approach.
This launch is more than just a test of our propulsion—it’s a reality check for the assumptions we’ve made. Whether everything works as expected or we encounter surprises, what matters is what we learn from it.
Beyond the Demo: What Comes Next
A successful demo will allow us to transition from development to production. The next step is scaling up manufacturing, with the goal of producing 20 flight-ready systems per year. This would enable commercial operators, defense applications, and deep-space missions to have a faster, more flexible propulsion option.
This mission is just one step in a much larger journey. There are still many challenges ahead, but the goal remains the same: to build a chemical propulsion that fit to the speed of modern space industry.
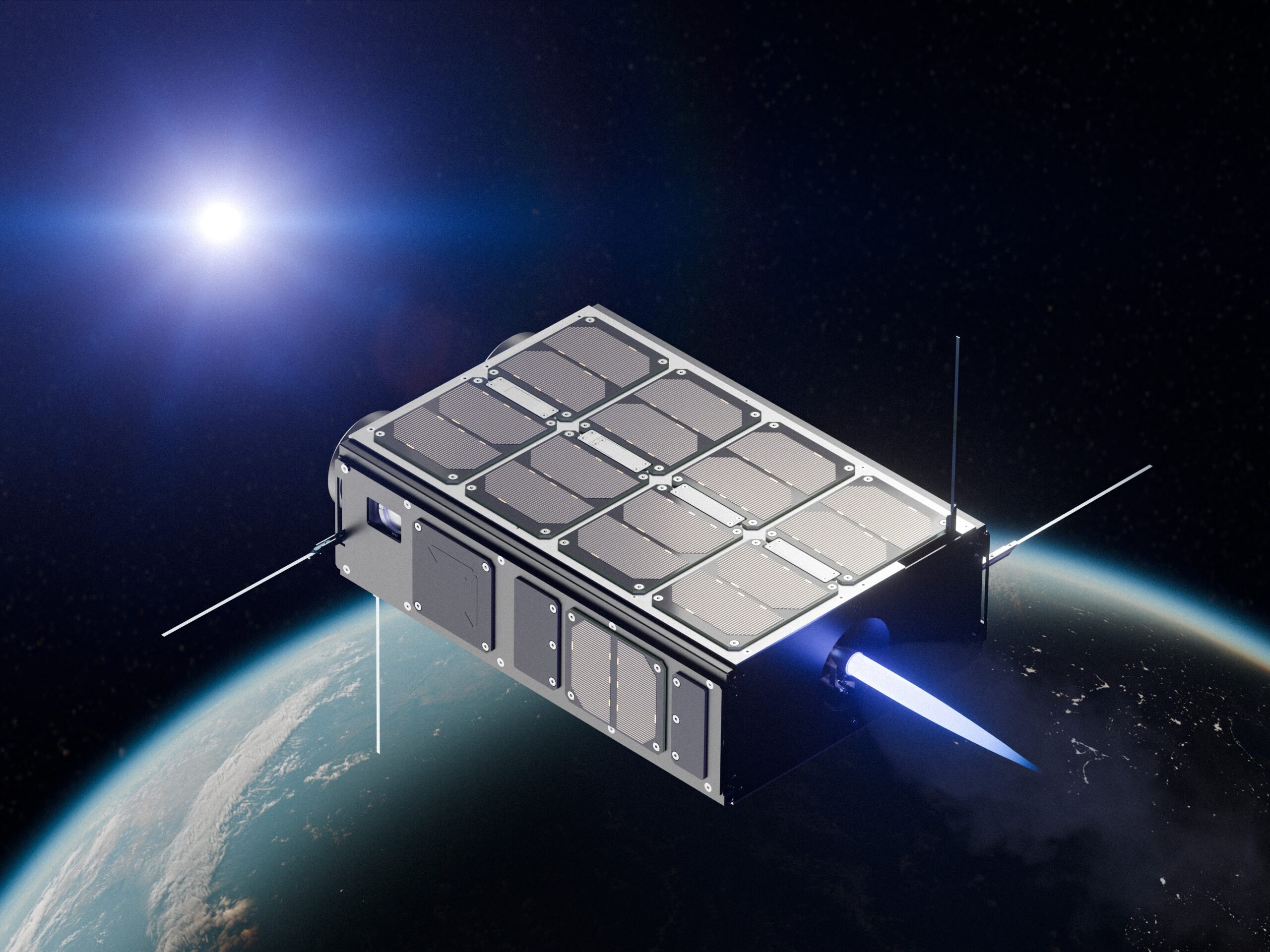