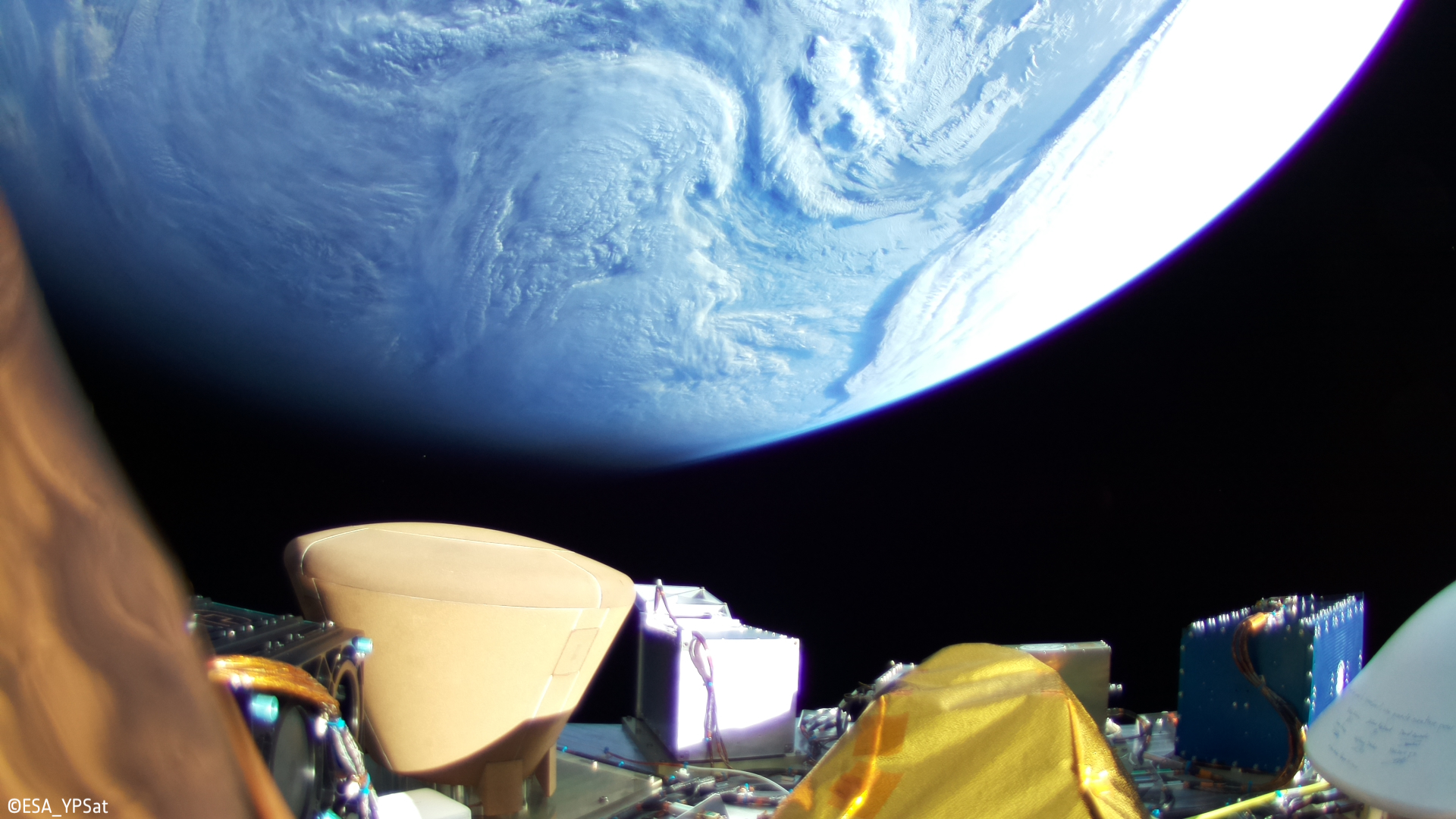
The recent issues with the Ariane 6 mission have highlighted a significant problem in space exploration: space debris.
While the Ariane 6 was designed to boost Europe’s space capabilities, its Auxiliary Power Unit (APU) failure left its upper stage as uncontrolled debris in orbit. This situation underscores the importance of addressing space debris and implementing effective propulsion systems for debris mitigation.
Space debris, or “space junk”, refers to defunct satellites, spent rocket stages and fragments from disintegration, erosion and collisions.
Even tiny pieces of debris travelling at high velocities pose a serious risk to active satellites, the International Space Station and future space missions. Without proper disposal, they can remain in orbit for years, increasing the likelihood of collisions and creating more debris.
In response to this problem, ESA has enforced strict Space Debris Mitigation Requirements.
Key points concerning satellites include:
- Reducing the maximum time in low-Earth orbits from 25 to 5 years for new ESA missions.
This means that if your satellite is orbiting above roughly 450 km, you must equip it with a propulsion system to ensure deorbiting, as atmospheric drag alone won’t suffice. - Ensuring satellites either re-enter the atmosphere or relocate to graveyard orbits that avoid operational regions for at least 100 years.
You can opt for a different orbit, but you will still need a propulsion system for this maneuver. - Designing satellites to disintegrate completely upon re-entry to minimise ground casualty risks.
You need to use demisable materials (those that burn up easily) in your satellite, which is especially important for propulsion systems. - Incorporating systems for external removal services to handle both cooperative and uncooperative scenarios.
This involves designing attachment points or interfaces that external removal services can latch onto for de-orbiting or repositioning. - The probability of successful disposal for satellites and launch vehicle stages must exceed 0.9 through to end of life.
Your satellite and propulsion system must be reliable at the end of the mission, which means that you need to think about an End of Life (EOL) performance. - Large constellations (100+ satellites) must meet stricter standards for collision avoidance and end-of-life disposal to ensure sustainable space operations.
Meeting regulations is easier with reliable chemical propulsion.
Only chemical propulsion gives the high thrust for quick maneuvers.
This capability is essential for promptly de-orbiting defunct or decommissioned satellites, reducing the time they spend as potential debris.
Using high-thrust ensures that de-orbiting maneuvers do not create additional problems due to short and rapid trajectories. In contrast, low-thrust electric propulsion systems require months for de-orbiting, increasing the risk of collision with other satellites due to constantly changing trajectory.
Long history of chemical propulsion in space means reliability.
Chemical propulsion has a long history of use in space missions, with well-understood technology and a robust component ecosystem. This reliability ensures that disposal maneuvers can be executed successfully, even in challenging conditions.
Green propellants make chemical propulsion safer than ever.
Recent developments have greatly improved the safety and handling of chemical propellants, addressing concerns about their toxicity. Green propellants, such as those based on nitrous oxide, offer reduced toxicity compared to traditional hydrazine. Recent years have seen significant progress and widespread market adoption of these safer alternatives, particularly nitrous oxide-based chemical propellants developed by companies such as Liftero.
These advances are helping to overcome the perception that chemical propulsion is inherently toxic and are demonstrating that it can be safe for widespread use.
With chemical propulsion, de-orbiting can be even 10 times cheaper.
While propellant loading into the satellite for chemical propulsion adds extra costs, the propellant itself is far cheaper than Xenon for electric propulsion—resulting in lower overall costs. Liftero use Nitrous Oxide, which is a well-known and readily available industrial gas used in a wide range of industries, and its cost is marginal.
Chemical propulsion requires minimal power regardless of thrust levels or tank size.
Chemical propulsion systems can be scaled and adapted for different sizes of satellites and missions. Unlike EP systems, chemical propulsion requires minimal power regardless of thrust levels or tank size. This allows the satellite to allocate its limited power supply to mission-critical activities such as imaging or communication. At the end of the satellite’s life, when power generation may be weak, chemical propulsion ensures that de-orbiting can still be accomplished effectively.
What About Other Propulsion Types?
Electric propulsion is not effective for rapid de-orbiting maneuvers.
Electric propulsion systems use energy to accelerate propellant particles, providing thrust. These systems impart higher velocities to the particles, resulting in significantly greater exhaust speeds compared to chemical propulsion. However, electric propulsion typically generates lower thrust because it can only accelerate a small amount of propellant at a time, requiring longer operational periods to achieve the same velocity change.
These systems are well-suited for fine-tuning satellite positions but are less effective for rapid deorbiting maneuvers needed to mitigate space debris.
Propellant-less propulsion suffers from low reliability and very limited control over satellite movements.
Propellant-less propulsion technologies, such as solar sails, tethers, and aerodynamic drag devices, harness natural forces like solar radiation pressure or atmospheric drag to produce thrust. While these technologies do not require onboard propellant, they generate very low thrust and don’t have high heritage in space missions.
If a system is to be installed on a satellite, it should ideally provide full control over the satellite’s movements, which propellant-less technologies currently do not offer.
Chemical propulsion is the most effective and reliable way to safely de-orbit your satellite and meet debris regulations.
Its high thrust, cost-efficiency and low toxicity make it the ideal solution for safely de-orbiting satellites. You can learn more about our advanced chemical propulsion systems and how they can meet your mission needs here.